Which Welding Methods Are Most Effective for Aluminium?
Aluminium welding is an essential process for a wide range of industries, from automotive to construction and manufacturing. As a lightweight yet strong metal, aluminium is often chosen for its durability and resistance to corrosion. However, welding aluminium requires specific skills and knowledge due to its unique properties. The key to achieving a strong, lasting weld is choosing the right welding method. But with several different techniques available, how do you decide which one is the most effective for your aluminium welding works?
In this blog, we will explore the most effective welding methods for aluminium, explaining each process, its advantages, and where it is best used. Whether you’re a professional welder or someone looking to take on a DIY project, understanding these methods will help you choose the best one for your aluminium welding needs.
Understanding Aluminium Welding
Before diving into the different welding methods, let’s take a moment to understand aluminium welding itself. Welding is the process of joining two or more pieces of metal by melting them at the interface and adding a filler material. In the case of aluminium welding, the process requires special techniques because aluminium behaves differently from other metals like steel.
Aluminium has a low melting point, and its high thermal conductivity means it can absorb heat quickly, which can make it tricky to weld. Additionally, aluminium has an oxide layer that forms on its surface when exposed to air. This oxide layer must be removed to ensure a clean and effective weld. The choice of welding method can impact the ease of this process and the overall quality of the weld.
Most Effective Aluminium Welding Methods
Now, let’s explore the most common and effective aluminium welding methods. These include:
- TIG Welding (Tungsten Inert Gas Welding)
- MIG Welding (Metal Inert Gas Welding)
- Stick Welding (Shielded Metal Arc Welding)
- Friction Stir Welding
- Gas Welding
Each of these methods has its unique advantages and best-use scenarios. Let’s look at them in detail.
TIG Welding (Tungsten Inert Gas Welding)
TIG welding is often considered the most precise and versatile method for aluminium welding works. It uses a non-consumable tungsten electrode to create an arc that melts the aluminium, which is then joined with the help of a filler rod. One of the key benefits of TIG welding is that it allows for the production of clean and strong welds, even on thin aluminium sheets.
Advantages of TIG Welding
- High Precision: TIG welding offers great control over the weld, making it ideal for fine, detailed work. It’s commonly used for intricate aluminium parts where appearance and strength are crucial.
- Clean Welds: Because the process involves an inert gas (usually argon) to shield the weld from contamination, the result is often a clean, smooth, and attractive weld.
- Versatility: TIG welding can be used on a variety of thicknesses, from thin aluminium sheets to thicker sections.
Best Uses for TIG Welding
TIG welding is typically used in industries such as aerospace, automotive, and manufacturing, where precision and appearance are important. It is perfect for welding thin aluminium, which is common in products like car parts, aircraft components, and precision machinery.
Disadvantages of TIG Welding
- Slower Process: TIG welding can be slower compared to other methods, making it less suitable for high-volume projects.
- Requires Skill: This process requires a skilled operator, as the technique can be more difficult to master than other welding methods.
MIG Welding (Metal Inert Gas Welding)
MIG welding, also known as Gas Metal Arc Welding (GMAW), is another popular method for aluminium welding works. Unlike TIG welding, MIG welding uses a continuous consumable wire as both the electrode and filler material. The wire is fed into the weld pool while an inert gas (typically argon) is used to shield the weld area.
Advantages of MIG Welding
- Faster Process: MIG welding is faster than TIG welding because the wire is continuously fed, which allows for quicker welds.
- Ease of Use: MIG welding is easier to learn and can be automated for large-scale operations.
- Good for Thick Aluminium: MIG welding works well for thicker aluminium sections, where high heat input is required.
Best Uses for MIG Welding
MIG welding is ideal for high-production environments and projects involving thicker aluminium pieces. It is commonly used in industries like automotive manufacturing and shipbuilding, where speed and efficiency are key.
Disadvantages of MIG Welding
- Less Precision: MIG welding is less precise than TIG welding, which means it may not be the best choice for delicate or highly detailed work.
- More Heat: MIG welding generates more heat, which can lead to distortion or burn-through in thin aluminium.
Stick Welding (Shielded Metal Arc Welding)
Stick welding, or Shielded Metal Arc Welding (SMAW), is one of the most common welding techniques used for a wide variety of metals, including aluminium. This method uses a consumable electrode that is coated with flux, which helps protect the weld area from contaminants in the air.
Advantages of Stick Welding
- Simple and Affordable: Stick welding is one of the simplest and most cost-effective methods for aluminium welding works. It doesn’t require expensive equipment and is perfect for DIY welders and small-scale operations.
- Works on Rusty or Dirty Materials: Stick welding is often used in situations where the aluminium surface isn’t perfectly clean. The flux coating on the electrode helps to shield the weld from contamination.
Best Uses for Stick Welding
Stick welding is best suited for outdoor and construction environments, where the equipment is durable and easy to transport. It’s also a great option for repair work or when dealing with older, rusted materials that other methods might struggle with.
Disadvantages of Stick Welding
- Less Precision: Stick welding is not as precise as TIG or MIG welding, making it unsuitable for detailed work.
- Poor Aesthetics: Stick welding typically produces welds that are less aesthetically pleasing compared to TIG or MIG welding.
Friction Stir Welding
Friction Stir Welding (FSW) is a relatively newer and innovative technique that has gained popularity in industries like aerospace and shipbuilding. This method uses a rotating tool to generate frictional heat, which softens the aluminium and allows it to be joined under pressure. No filler material is required, and the weld is formed by mechanically stirring the material.
Advantages of Friction Stir Welding
- Strong Welds: Friction stir welding produces strong, high-quality welds with minimal distortion.
- No Filler Material Needed: This method does not require any filler material, which can make it more efficient and cost-effective.
- Excellent for Thick Materials: FSW is highly effective for welding thick aluminium sections, which is why it is used in large-scale manufacturing like shipbuilding and rail transport.
Best Uses for Friction Stir Welding
Friction stir welding is commonly used in aerospace, automotive, and shipbuilding industries for projects that require joining thick aluminium sheets, such as aircraft wings, boat hulls, and train bodies.
Disadvantages of Friction Stir Welding
- Requires Specialized Equipment: FSW requires specialized machines and tools, making it more costly than other welding methods.
- Not Suitable for Thin Aluminium: While it’s great for thick materials, FSW is not suitable for thin sheets of aluminium.
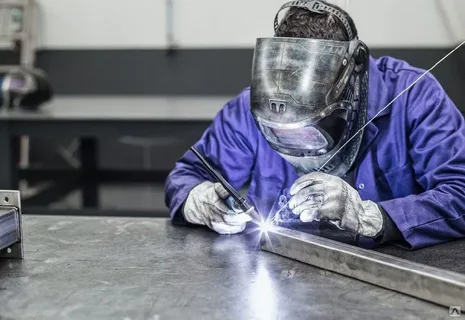
Gas Welding
Gas welding, also known as oxy-acetylene welding, is one of the oldest welding methods. It involves using a flame from an oxy-acetylene torch to heat the aluminium until it melts. A filler rod is then added to form the weld.
Advantages of Gas Welding
- Simple and Portable: Gas welding equipment is relatively simple and portable, making it suitable for a wide range of applications.
- Good for Thin Materials: This method works well for thin aluminium materials, as it provides excellent control over the heat input.
Best Uses for Gas Welding
Gas welding is often used for small-scale repairs and light fabrication work. It’s ideal for situations where portability is important, such as field repairs or remote locations.
Disadvantages of Gas Welding
- Slower Process: Gas welding is slower than other methods, making it less ideal for high-volume projects.
- Limited Strength: While it works well for thin materials, the weld strength may not be as high as other methods like TIG or MIG welding.
Choosing the Right Welding Method for Your Project
Choosing the right welding method for your aluminium welding works depends on several factors, including the thickness of the material, the desired weld strength, the complexity of the project, and the available equipment. Here are some general guidelines to help you choose:
- For Thin Aluminium Sheets: TIG welding or gas welding is ideal for thin aluminium materials where precision and minimal heat input are required.
- For Thick Aluminium Sections: MIG welding or Friction Stir Welding works best for thicker aluminium, where higher heat input is needed.
- For High-Volume Production: MIG welding is an efficient choice for large-scale, high-production environments.
- For Precision and Fine Work: TIG welding is the best option for projects requiring a high level of precision and a clean, aesthetically pleasing weld.
- For Budget-Friendly, DIY Projects: Stick welding or gas welding is a cost-effective and accessible option for smaller projects and repairs.
Conclusion
Aluminium welding is a crucial process that requires selecting the right welding method based on the material thickness, project requirements, and desired weld quality. Whether you’re welding for industrial purposes or tackling a DIY repair, understanding the different welding methods will help ensure you achieve the best results.
TIG, MIG, Stick, Friction Stir, and Gas Welding are all effective techniques for aluminium welding works, each offering unique advantages for specific applications. By considering the nature of your project and the equipment available, you can choose the best method to ensure a strong, durable, and clean weld.
By making the right choice, you can improve the efficiency, quality, and cost-effectiveness of your aluminium welding projects..
For More Insightful Articles Related To This Topic, Feel Free To Visit: freshvoicehub.
Post Comment