How Do Liquid Ring Vacuum Pumps Handle Corrosive Gases?
Industries that address chemical substances and gases, inclusive of pharmaceuticals, meals processing, and petrochemicals, frequently encounter corrosive gases which can harm system. Using the proper generation to address these gases effectively whilst preserving system integrity is important. This is in which liquid ring vacuum pumps are available. These pumps are designed to manage moist, grimy, or corrosive gases without the operational issues confronted with the aid of conventional systems. In this text, we explore how liquid ring vacuum pumps take care of corrosive gases, their packages, and the way they paintings along air cooled warmness exchangers to make sure top-rated overall performance.
Understanding Liquid Ring Vacuum Pumps
Liquid ring vacuum pumps are rotary displacement pumps that use a rotating impeller and a sealing liquid, commonly water or other well-suited fluids, to create a vacuum. As the impeller spins, the liquid bureaucracy a hoop within the casing, trapping and compressing gases in the pump chambers. These pumps are known for his or her potential to deal with gases with high moisture content material, such as corrosive vapors.
Challenges of Managing Corrosive Gases
Corrosive gases, along with chlorine, sulfur dioxide, or hydrogen chloride, can be distinctly reactive and motive severe damage to machinery. Traditional vacuum pumps face demanding situations like:
- Corrosion and Erosion: Metal surfaces in direct contact with corrosive gases can degrade.
- Seal Failures: Gases can motive seals to interrupt down, main to leaks.
- High Maintenance Costs: Frequent restore and replacement of parts growth downtime and prices.
These demanding situations make liquid ring vacuum pumps an wonderful choice for handling such gases because they offer a more secure and greater green answer.
How Liquid Ring Vacuum Pumps Handle Corrosive Gases
Sealing Liquid Selection
The key characteristic of liquid ring vacuum pumps is the use of a sealing liquid. The choice of liquid is crucial whilst coping with corrosive gases. While water is normally used, different fluids like oil, glycol, or chemically resistant drinks may be employed to neutralize corrosive consequences.
Non-Metallic Components
Many pumps designed for corrosive environments incorporate non-metal or lined components. This minimizes direct contact among the pump’s metal elements and the gases, decreasing corrosion.
Closed-Loop Systems
In some industries, a closed-loop device is implemented to recirculate the sealing fluid, which prevents environmental publicity to poisonous or corrosive gases and decreases waste.
Durable Materials and Coatings
Components like impellers and casings may be coated with resistant materials along the lines of Teflon, stainless steel, or ceramic to prevent corrosion. These coatings enlarge the existence of the pump and make sure it continues to operate smoothly even underneath harsh conditions.
Applications of Liquid Ring Vacuum Pumps in Handling Corrosive Gases
Industries that need to manipulate corrosive gases thoroughly depend heavily on liquid ring vacuum pumps. Some key packages include:
- Chemical Manufacturing: Removing corrosive gases throughout the manufacturing of chemicals like hydrochloric acid.
- Pharmaceuticals: Handling solvents and gases in production techniques without contamination.
- Oil & Gas: Managing dangerous gases in the course of refining operations.
- Food Processing: Vacuum distillation approaches that contain reactive gases.
Enhancing Pump Efficiency with Air Cooled Heat Exchangers
When managing corrosive gases, maintaining the precise operating temperature of the liquid ring vacuum pump is important. This is in which air cooled heat exchangers come into play. These warmness exchangers remove warmness from the pump’s circulating fluid, preventing it from overheating and ensuring regular overall performance.
Some advantages of integrating air cooled warmness exchangers encompass:
- Reduced Energy Consumption: Air-cooled structures require no water, lowering application prices.
- Minimal Maintenance: These systems are less difficult to maintain than water-cooled warmth exchangers.
- Environmentally Friendly: No wastewater discharge, which aligns with sustainability goals.
Maintenance Practices for Liquid Ring Vacuum Pumps
Regular maintenance is important to keep liquid ring vacuum pumps in surest situation, in particular whilst coping with corrosive gases. Key practices consist of:
- Monitoring Sealing Fluid Quality: Regularly analyzing and replacing the sealing fluid prevents contamination and corrosion within the pump.
- Inspecting for Corrosion: Routine inspections of inner parts can pick out early signs and symptoms of corrosion, permitting well timed upkeep.
- Cleaning and Flushing: Periodically flushing the pump gadget eliminates any deposits or buildup due to corrosive gases.
- Temperature Management: Using air cooled warmth exchangers guarantees that the pump operates within the encouraged temperature variety, preventing thermal strain.
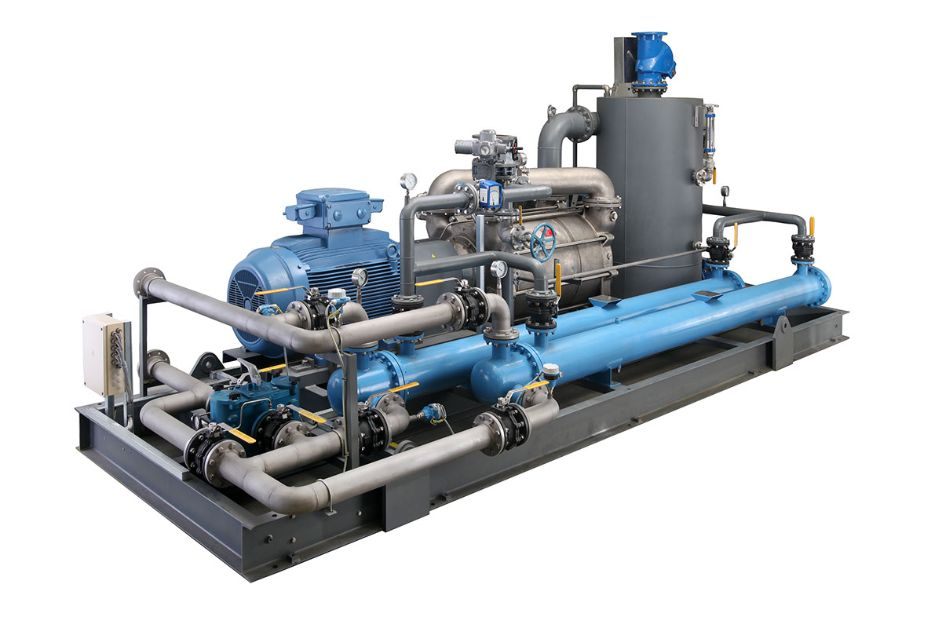
Conclusion
Handling corrosive gases calls for strong and reliable device. Liquid ring vacuum pumps are designed to control such gases efficaciously using sealing liquids, corrosion-resistant materials, and superior coatings. When paired with air cooled heat exchangers, those pumps achieve even better performance and sturdiness, making them perfect for industries handling harsh chemical environments. Proper protection guarantees those structures remain reliable and fee-powerful, contributing to clean business operations for years.
Whether you’re in chemical production or meals processing, making an investment in nice device like liquid ring vacuum pumps is critical to make sure protection, efficiency, and environmental compliance.
Post Comment